1 / 2
Schedule 40 Spiral Welded Carbon Steel Pipe DN200 to DN900
- Model
- schedule 40 spiral welded steel pipe
Item specifics
- Usage
- Oil and Gas Delivery
- Surface
- Black/Painted/Galvanized
- Material
- Q235/Q345,STK400/STK500,ST37/ST52,S235JR/S275JR
- Length
- 1-12m
Review
Description
SCH40 Spiral Welded Steel Pipe Description
The schedule 40 spiral welded carbon steel pipe is available in various sizes, ranging from 219mm to 2000mm in diameter. These pipes are commonly used in industrial applications for conveying fluids and gases. The schedule 40 designation indicates the wall thickness of the pipe, which is important for determining the pressure rating and structural integrity of the pipe. It's important to consult with a supplier or manufacturer to ensure that the specific size and specifications of the pipe meet the requirements of your project.
Nominal Pipe Size
|
Outside Diameter
|
Thickness Schedule 40
|
|
Inch
|
mm
|
mm
|
mm
|
8
|
200
|
219.1
|
8.18
|
10 | 250 | 273.1 | 9.27 |
12 | 300 | 323.9 | 10.31 |
14 | 350 | 355.6 | 11.13 |
16 | 400 | 406.4 | 12.7 |
18
|
450
|
457.2
|
14.27
|
20 | 500 | 508 | 15.09 |
22 | 550 | 558.8 | |
24 | 600 | 609.6 | 17.48 |
26 | 650 | 660.4 | |
28 | 700 | 711.2 | |
30 | 750 | 762 | |
32 | 800 | 812.8 | 17.48 |
34 | 850 | 863.6 | 17.48 |
36 | 900 | 914.4 | 19.05 |
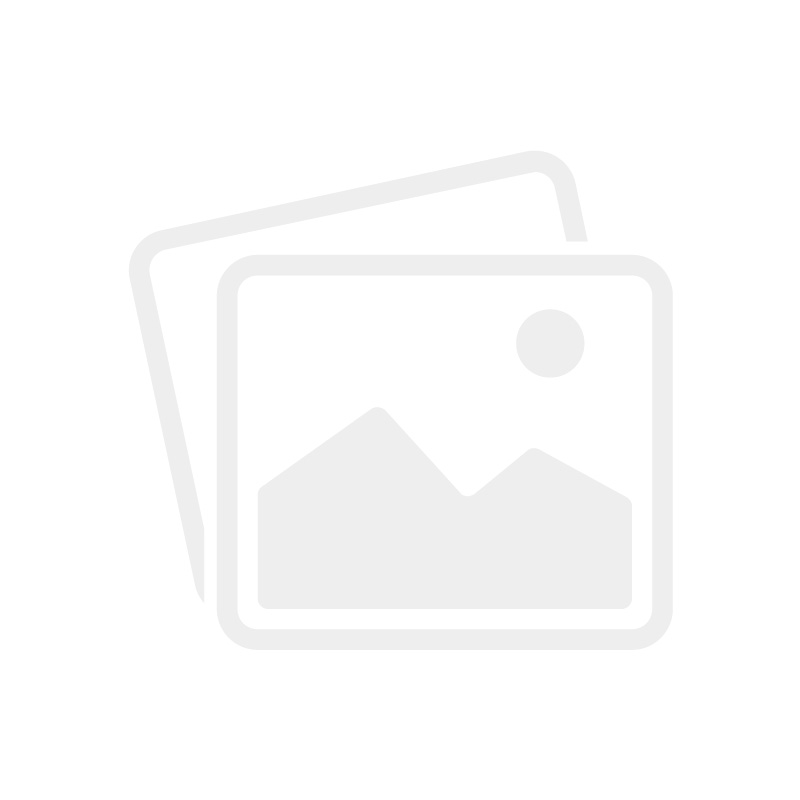
Schedule 40 Spiral Welded Steel Pipe
Material: Grade B, and so on.
Surface Treatment: Natural black, Painted, Galvanized, 3PE, FBE
Pipe Ends Treatment: Beveled or Flanged
Pipe Length: 5.8m, 6m or 12m or cut into short length according to requirement.
Usage: Oil and gas delivery pipeline, Pipe pile, Water delivery pipeline
Schedule 40 Spiral Welded Steel Pipe Production Line
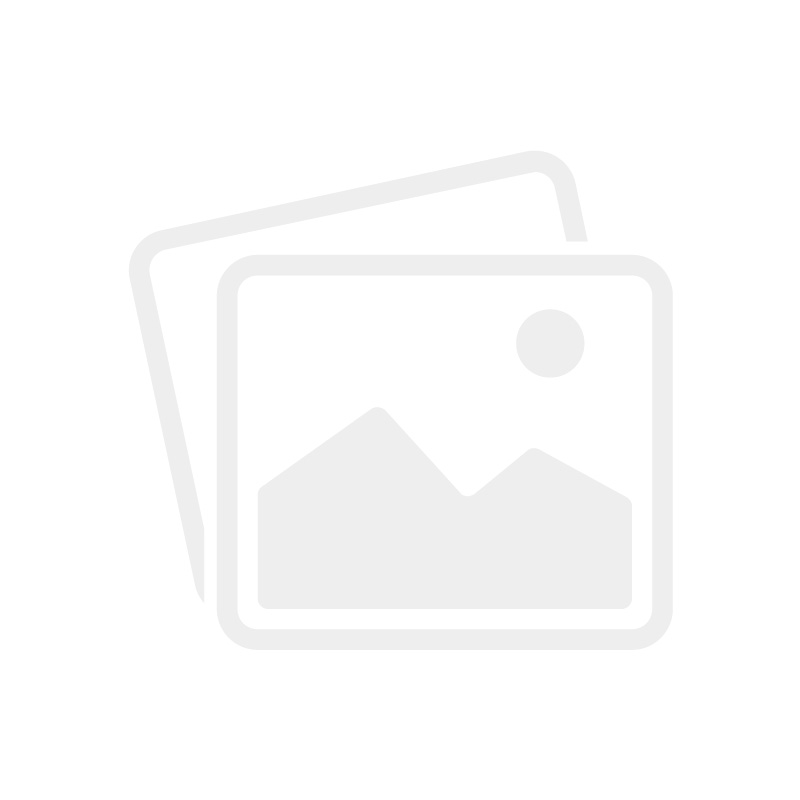
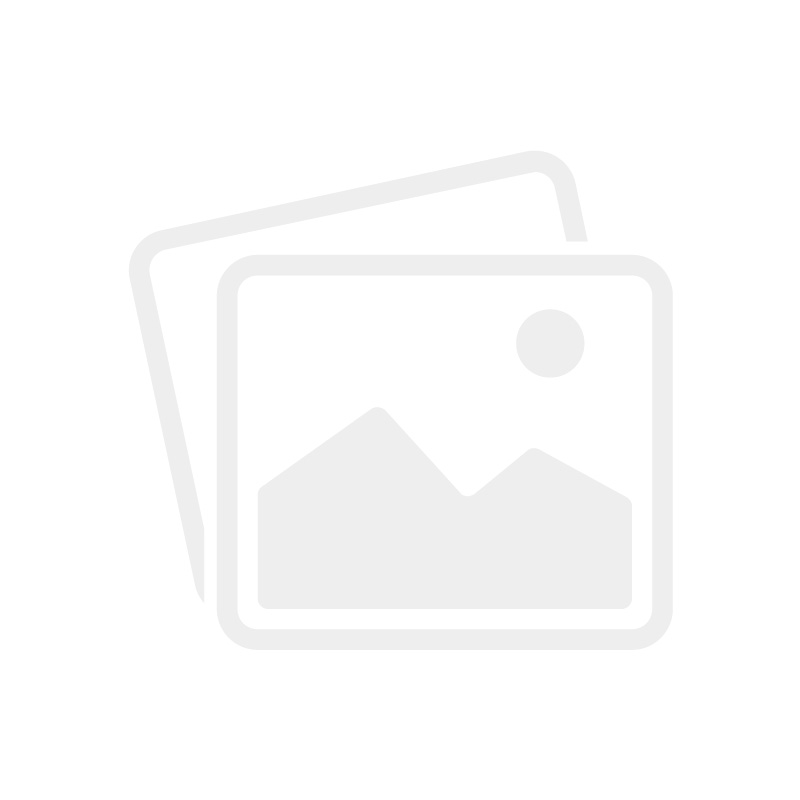
Spiral Welded Steel Pipe Quality Test:
Dimensional Inspection: checking the outer diameter, wall thickness, and length of the pipe to ensure they meet the specified tolerances.
Visual Inspection: examining the surface of the pipe for any defects, such as cracks, pits, or other imperfections.
Mechanical and Chemical Testing: such as tensile strength, yield strength, and elongation to ensure the pipe meets the required mechanical properties. and chemical composition of the steel.
Non-Destructive Testing (NDT): NDT methods such as ultrasonic testing, radiographic testing, or magnetic particle inspection can be used to detect internal defects or discontinuities in the weld.
Hydraulic Pressure Testing: This involves subjecting the pipe to hydraulic or pneumatic pressure to ensure it can withstand the specified operating pressures.
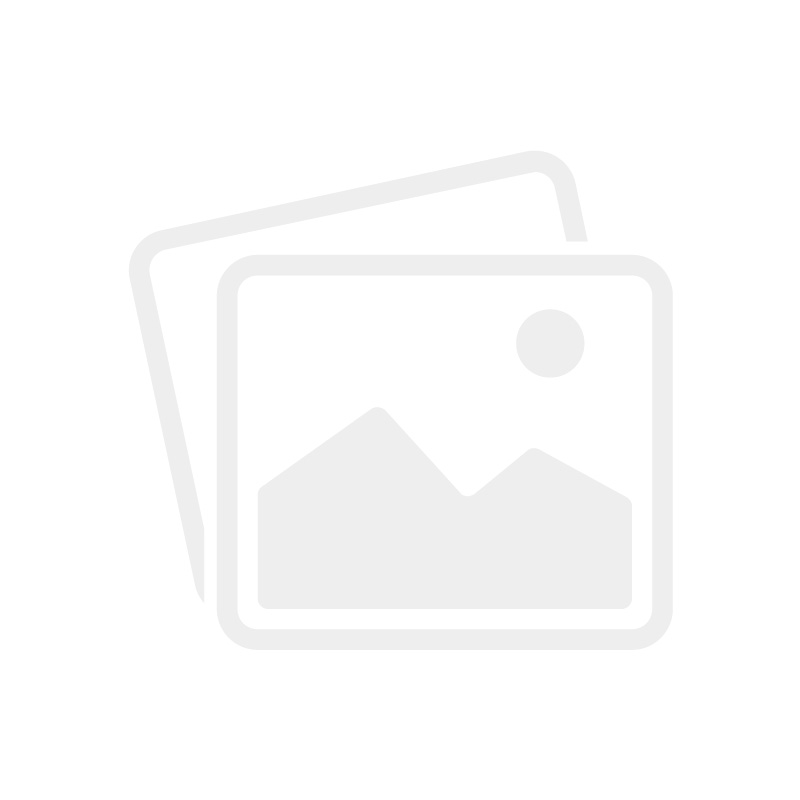
Schedule 40 SSAW Steel Pipe Transportation
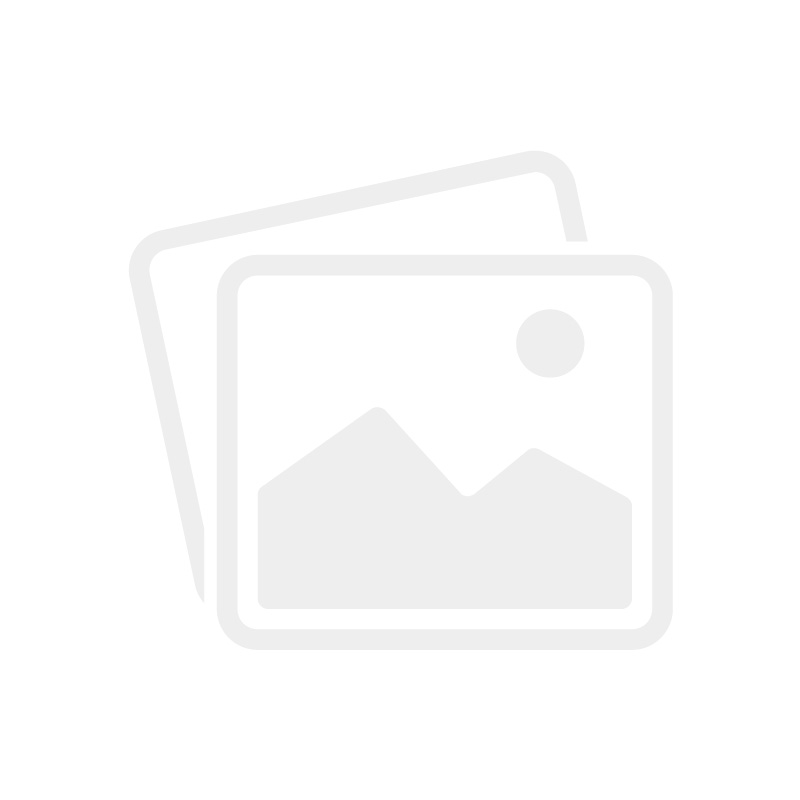
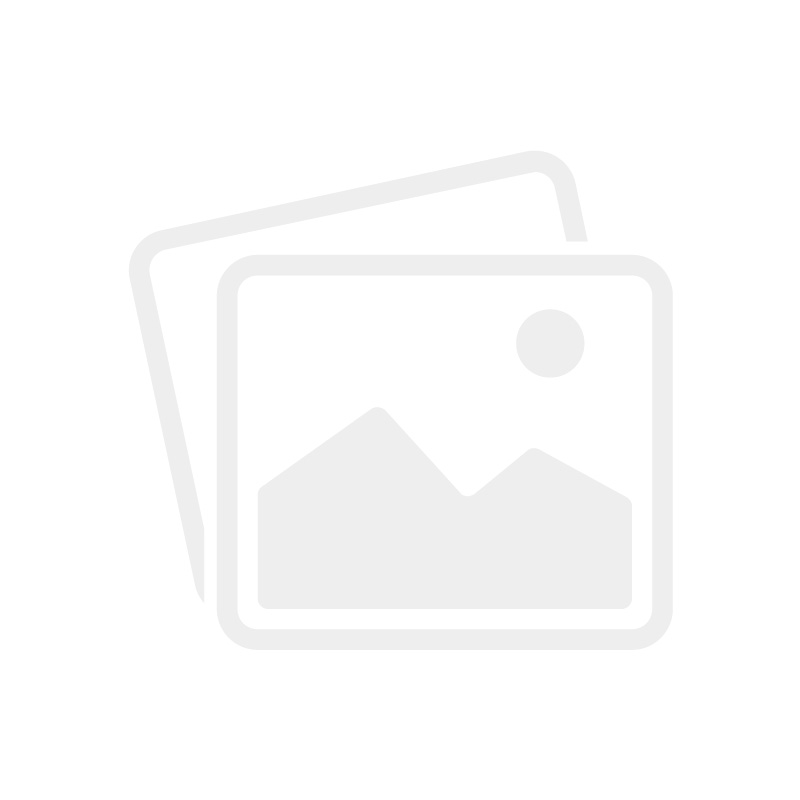
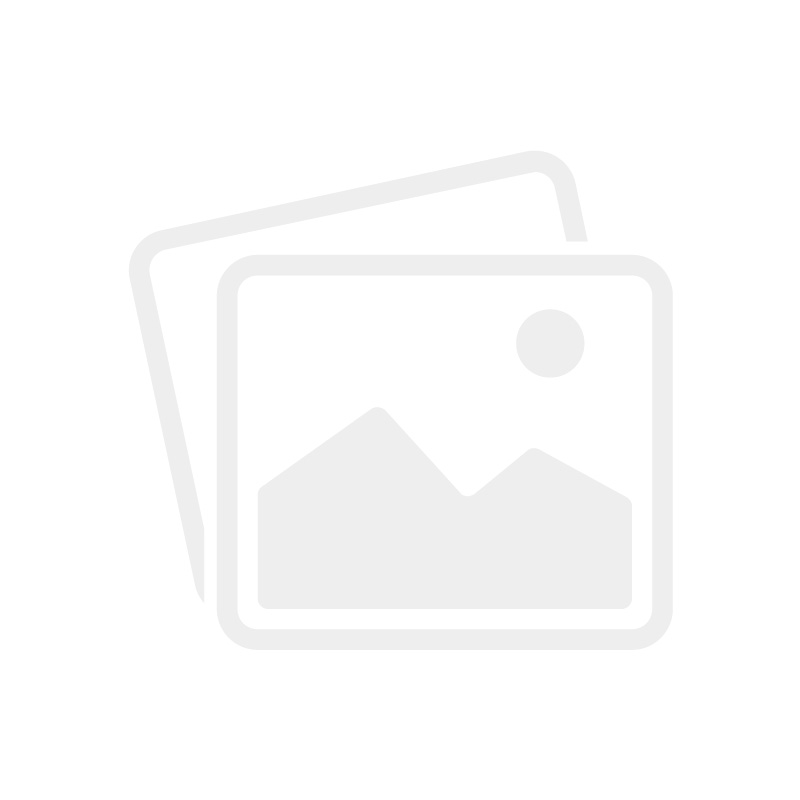